SERVICES
Gear Lubricants Testing
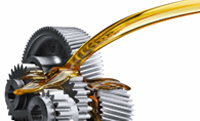
Regular lubrication is required to maintain optimal performance in equipment & machinery yet serious lubrication problems are widespread. The results driven solution to this lubrication problem epidemic are polymer infused lubricants and a systematic approach to the maintenance program.
Typically petroleum lubricant formulations contain forty to sixty carbon atoms. Polymer infusion bumps this carbon profile up to 400 to 4000 atoms which creates a stronger, longer chain of atoms. This longer chain produces many benefits that standard petroleum lubricants cannot provide not the least of which is the ability to reduce or completely stop leaks, even around worn seals which extends the greasing/lubricating cycle.
Due to this long chain we see robust useful life of between 3 to 5 times that of typical conventional lubricants plus a considerable reduction in friction and heat. This reduction of friction plays out in another way as well; reducing the energy required to operate the machinery or equipment. We have seen a reduction of up to 15% in running amperage in some cases!
Lubricant Quality Scanning
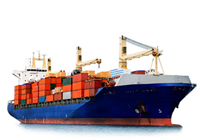
Monitoring lubricant condition and quality helps protect expensive large engines and equipment from costly failure and down-time.
Shipping, maritime, offshore, and others depend upon Intertek’s ShipCare lubricant quality scanning (LQS) services to ensure the integrity of their lubricants and operating systems.
WIth over 25 years of experience, Intertek goes beyond simply supplying test data; we provide important service recommendations based on the test data obtained from our laboratory analysis. Lubricant testing data, collected over time, identifies and tracks potential problems related to trends in engine and parts wear, based on the composition and amounts of contaminants found, providing an early-warning system to help avoid costly engine shutdowns.
When interpreting the lubricant analysis, Intertek data consultants look closely at critical parameters, providing essential information that will save costly down-time and emergency repairs.Intertek oil condition monitoring technical consultants offer guidance, explain test results, discuss maintenance history, and suggest corrective actions when needed.
Lubricant Qualification Testing

Lubricants is one of the largest independent lubricating oil brands in Europe.Lubricants produces and markets a comprehensive selection of high quality lubricants and specialties which find their way in a wide range of applications. The products are developed and produced by specialists who can choose from a wide variety of base oils and additives, to obtain lubricants meeting the latest standards of the Original Equipment Manufacturers(OEM’s) and International Standardization Committies.
Lubricants are all produced in one of the largest and most sophisticated lubricant blending plants in the Netherlands. This blending plant with it’s annual production capacity of 130.000 Metric Tons of finished lubricants has a base oil storage capacity 17 million litres, more than 60 tanks for the storage of finished products and several warehouses for storing packaged products.
Ferrography Testing
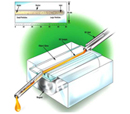
Ferrography testing by Intertek provides non-intrusive evaluation of lubricated components while the equipment is in a running state. Intertek experts offer ferrographic failure analysis to clients across industries and markets. Ferrography analysis test data allows clients to avoid costly machine shut-downs and extend component life by taking preventative actions when early-warning abnormal wear is found. By monitoring particles generated by wear or environmental contamination, Intertek ferrography experts are able to to detect the critical stage of accelerated wear that precedes costly and dangerous component failures. Ferrographic analyses determines the number, size and shape of wear particles.After the samples are analyzed by Intertek, the client receives a comprehensive diagnosis report by email or in hard copy format. The detailed report includes interpretation and a full color microscope photo of the wear particles.
Oils and Fluids Testing
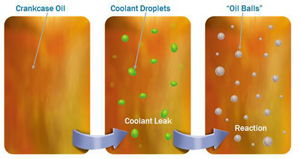
The oil analysis report we received from our lab showed elevated levels of sodium and potassium in our engine oil. This oil has also become significantly thicker. What could be causing this to occur?
There are multiple sources for the sodium found in your diesel engine oil. Based on your operational environment and equipment type, you should be able to narrow this down to a smaller list of causes. Potential sources of sodium include coolant, salt water, additives, grease thickener, base stocks, dirt and road salt.
On the other hand, potassium has only one real major source when found in engine oil — antifreeze. Other key elements that you will want to look for are boron, chromium, phosphorus and silicon. All of these elements are associated with antifreeze and, if found in engine oil, can be an indicator that you have a coolant leak.
Wear Metals Testing
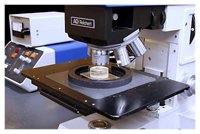
Wear metals testing in lubricants, oils and other machine fluids helps clients avoid expensive damage and downtime to high value engines, gears, generators, turbines and other important equipment.
Early detection of wear metals in lubricants and greases improves machinery reliability, especially if done as part of a professional oil condition monitoring program.
Intertek wear metals testing detects the presence of suspected metal wear contamination, down to parts per million range (ppm), and is an early warning for impending machinery damage or failure.
Oil Analysis
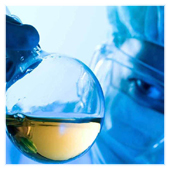
Oil analysis testing labs analyze a wide range of oil based products. Supporting client oil condition and predictive maintenance programs, Intertek oil tests are performed to ASTM, ISO, IEC, IP, in-house, client, and other industry standards. Oil analysis is fast, efficient, and cost-effective.
Intertek’s global network of oil analysis laboratories tests lubricants ranging from the support of OEM and operator equipment condition monitoring programs, small-batches and even single samples. Oil analysis capabilities include routine and non-routine testing, troubleshooting, R&D, contamination detection, and detailed chemical trace analysis. Shipment of the samples for testing to the appropriate laboratory can be easily arranged as and when required.